医疗器械生产工艺是确保医疗产品质量、安全性和可靠性的核心环节。随着全球医疗需求的不断增长,医疗器械行业也经历了快速的发展和技术创新。医疗器械不仅仅是医生手中的工具,更是患者生命安全的保障。在这背后,涉及到复杂的设计、严谨的生产流程和严格的质量控制。因此,掌握先进的医疗器械生产工艺,是提升产品竞争力和确保合规性的关键。
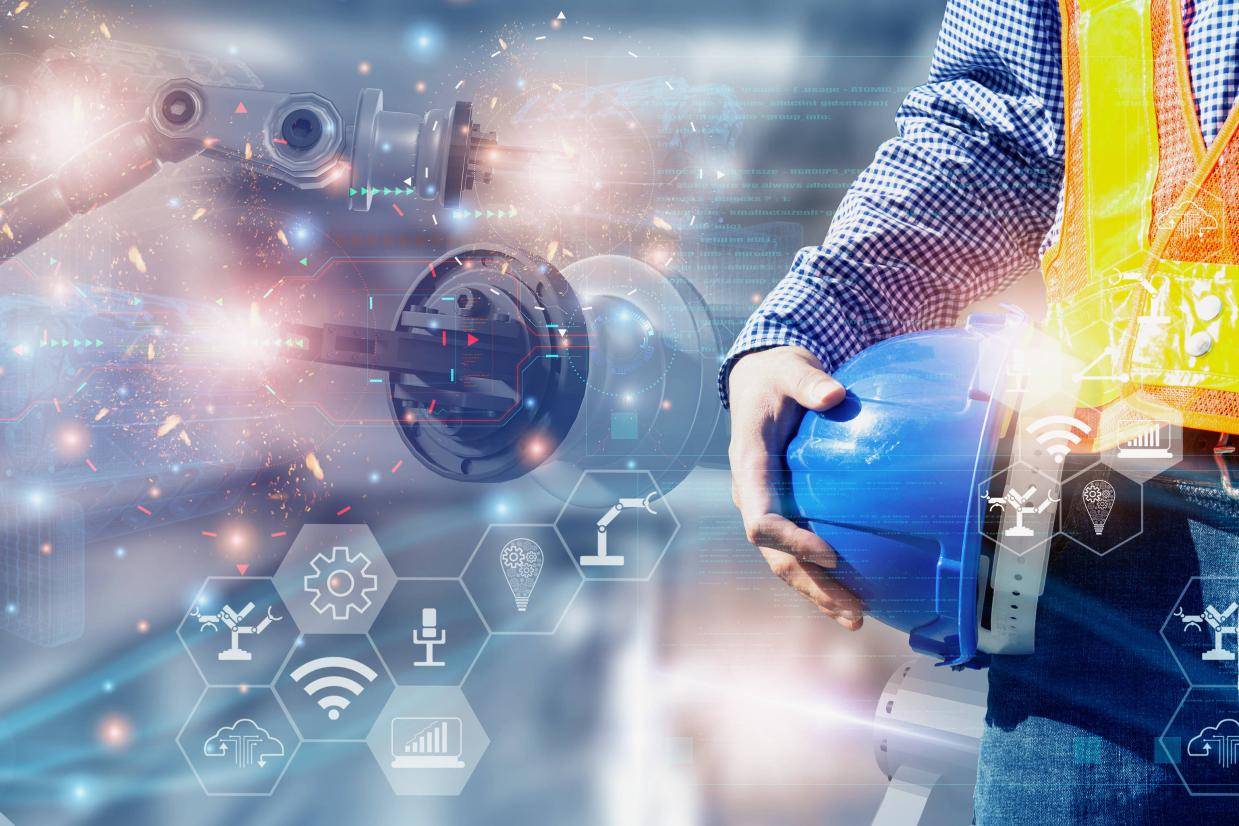
一、医疗器械的设计开发
医疗器械的生产工艺始于设计开发阶段。这一阶段不仅关乎产品的功能性,还关乎其安全性、适用性和便捷性。在设计医疗器械时,首先要确保产品能够满足特定的临床需求。设计师和工程师需要与医生、患者和其他相关人员进行充分沟通,以确保产品能够有效解决实际问题。
在设计阶段,产品的结构、功能、使用材料、可操作性等都需要经过精确的计算和模拟。例如,外科手术器械需要保证锋利且不易生锈,而影像诊断设备则需要有足够的精度和图像清晰度。符合人体工程学设计的考虑也至关重要,确保产品不仅能够提高效率,还能减轻医护人员和患者的使用负担。
设计开发阶段的另一个关键环节是产品验证。通过原型制作和实验验证,设计方案需要在实际使用条件下进行检验,确保产品能够满足功能要求并保持安全性。这一过程通常包括模拟试验、机械强度测试、材料疲劳测试等。所有测试结果都将成为后续生产工艺制定的依据。
二、材料选择与工艺规划
材料的选择是医疗器械生产中的一个重要环节。不同种类的医疗器械对材料的要求各不相同,材料的生物相容性、机械性能、耐腐蚀性等因素都会直接影响到器械的使用效果和患者的安全。
例如,在植入类医疗器械中,如人工关节和心脏支架,材料的生物相容性尤为重要。这些产品需要与人体组织和体液长期接触,因此必须选择不容易引起过敏反应或其他副作用的材料。常见的材料有不锈钢、钛合金、聚合物等。
对于一次性使用的医疗器械,如注射器和导尿管,材料的耐用性和无毒性是首要考虑的因素。在这一类产品中,通常选择医用级塑料、橡胶等材料,这些材料不仅具有良好的生物相容性,还能保证在使用过程中不产生有害物质。
生产工艺的规划也直接影响材料的选择。例如,在塑料注射成型过程中,材料的流动性、温度稳定性等都需要考虑在内,以确保最终产品的精度和一致性。
三、制造过程的关键技术
制造过程是医疗器械生产工艺中最为关键的部分。不同种类的医疗器械,其制造工艺和流程也有所不同,但基本的生产步骤通常包括注塑成型、激光切割、焊接、表面处理等。
注塑成型:注塑成型是生产医疗器械中许多塑料部件的常见工艺,尤其是在生产一次性使用的产品时。通过高温加热,将塑料熔化后注入模具中,待其冷却后即可得到所需形状的部件。注塑成型工艺具有高效率、精度高等优点,适合大规模生产。
激光切割与打标:激光切割技术广泛应用于医疗器械中,特别是在需要高精度加工的领域,如外科手术器械、人工植入物等。激光切割技术能够在不接触材料的情况下进行精密加工,避免了传统机械加工中可能出现的材料损伤或精度误差。激光打标技术也被用于在产品上刻印序列号、生产日期等信息,保证产品的追溯性。
焊接技术:在某些医疗器械中,尤其是需要高强度连接的部件,焊接技术是不可或缺的。例如,某些医疗仪器的金属外壳和内部组件需要通过激光焊接或高频焊接进行连接,以确保结构牢固且不会因使用过程中的应力而发生变形。
表面处理:医疗器械的表面处理同样至关重要,尤其是直接与人体接触的产品。表面处理工艺包括电镀、涂层、氧化等,目的是提高器械的耐腐蚀性、抗菌性能和美观性。例如,某些植入物可能会采用抗菌涂层,以减少感染的风险。
四、质量控制与检验
医疗器械的生产过程中,质量控制是每个环节的重中之重。从原材料的采购、生产过程的每一道工序,到最终产品的出厂检验,都需要严格的质量控制。
原材料检验:所有用于生产医疗器械的原材料,都需要经过严格的检验,确保其质量符合要求。包括材料的化学成分、物理性能、尺寸精度等方面的检验。只有合格的原材料才能进入生产流程,避免不合格材料导致产品质量问题。
过程控制:在制造过程中,每个工序的操作都需要进行实时监控和记录。生产线上的设备要定期校准,确保精度和稳定性。操作人员也需要经过严格的培训,确保每个环节都按照标准流程执行。
最终检验:每一批次的医疗器械产品都需要进行全面的质量检验。常见的检验项目包括功能测试、尺寸测试、外观检查等。对于某些特别的医疗器械,如植入物、诊断设备等,还需要进行更加细致的性能验证,确保其在临床使用中的安全性和有效性。
通过这些精细化的质量控制措施,确保每一件医疗器械都能达到国家和行业的质量标准,进而保障患者的生命安全和治疗效果。
【说明】以上文中所展示的图片是同心雁S-ERP的操作界面截图,点击右侧“在线咨询”或者“立即试用”按钮,获软件系统演示方案~