在医疗器械快速发展的今天,产品质量和生产效率已成为企业核心竞争力的关键因素。返工流程的不当管理可能导致成本上升、效率降低甚至影响产品质量。本文将深入探讨医疗器械生产返工流程的优化策略,为企业提供切实可行的解决方案,助力企业提升整体竞争力。
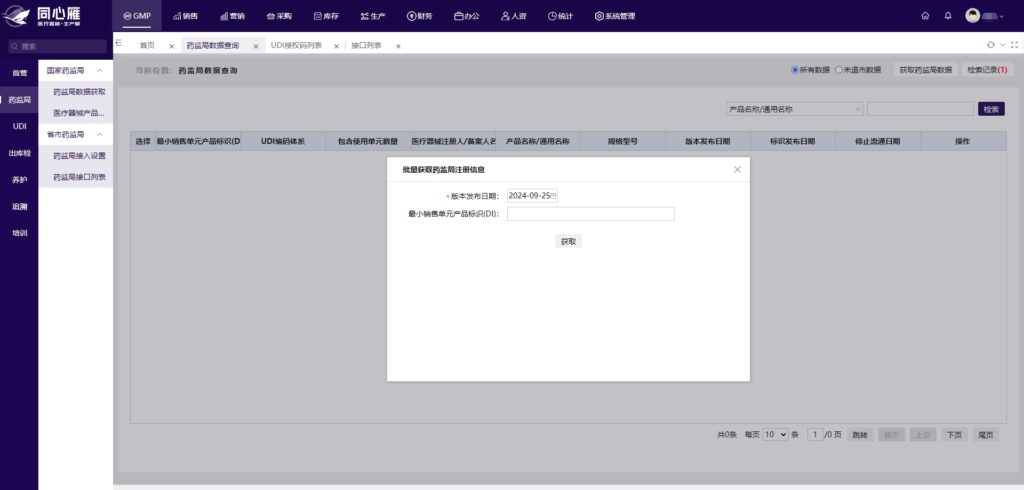
打破常规,优化医疗器械生产返工流程
在医疗器械的生产过程中,返工流程始终是一个不容忽视的问题。返工不仅仅是对不合格品的再次加工,更是一种对生产效率和产品质量的双重考验。传统的返工流程往往以事后处理为主,导致返工成本居高不下,同时影响生产节奏和客户满意度。
为了真正实现返工流程的优化,我们需要从源头抓起,建立预防性思维。具体来说,可以从以下几个方面入手:
深入原因分析
在发现问题时,首先要做的不是直接进行返工,而是深入分析问题的根本原因。通过rootcauseanalysis(因果分析),我们可以找出产品质量不稳定的核心问题,从而制定针对性的解决方案。
过程中的缺陷预防
在生产过程中,及时发现并纠正潜在问题至关重要。采用预防性测试和严格的质量控制措施,可以最大限度地减少返工的可能性。例如,在关键工步设置严格检测,确保每一道工序都符合标准。
引入自动化检测技术
随着技术的进步,自动化检测设备已广泛应用于医疗器械生产中。这些设备不仅可以快速检测产品质量,还能在发现问题时立即触发警报,减少人为错误的发生。
优化返工流程
在确认问题原因后,根据具体情况优化返工流程。例如,可以采用快速修复技术,缩短返工时间;或者将返工品与其他合格品分开处理,避免交叉污染。
通过以上措施,我们可以将返的返工率显著降低,同时提高生产效率。更重要的是,这将为企业节省大量的返工成本,同时提升客户对产品的信任度。
从源头抓起,构建高效医疗器械返工管理体系
要实现返工流程的优化,建立高效的质量管理体系是基础。只有有了良好的管理体系,才能确保每一个环节都符合标准,从而降低返工率。
源头管理,从原材料开始
原材料的质量是生产质量的基础。企业应建立严格的原材料采购管理制度,对供应商进行资质审核,并对原材料进行全生命周期的跟踪。只有源头把控住了,后续的生产才有保障。
严格的质量控制
在生产过程中,每一道工序都应有严格的质量控制措施。例如,在关键工步设置专门的质量检验员,采取抽样检验或全数检验的方式,确保每一批次都符合标准。
建立质量追溯体系
在生产过程中,每个产品的生产记录都应有详细的电子档案。通过构建质量追溯系统,企业可以快速定位问题,找到改进的方案。例如,某台设备出现故障,通过追溯系统可以追溯到原材料的批次,进而快速解决问题。
持续优化,实现精准修复
�.jsxdans&\n只有不断优化返工流程,才能实现精准修复。企业应建立返工后的快速修复机制,例如采用模块化设计,使得修复工作更加高效。定期对生产流程进行审查,找出改进点,确保返工率持续下降。
跨部门协作,共享经验
在返工过程中,不同部门的经验和教训可以互相借鉴。例如,质量部门可以为生产部门提供技术支持,生产部门的经验又可以反哺质量部门。通过建立共享机制,企业可以不断优化返工流程,提升整体效率。
总结
医疗器械的生产返工流程优化是企业提升竞争力的关键。通过深入分析问题根源,从源头抓起,建立全面的质量管理体系,企业可以有效降低返工率,提高生产效率和产品质量。未来,随着技术的不断进步和管理理念的更新,我们有理由相信,医疗器械的生产流程将更加高效、更加可靠。
【说明】以上文中所展示的图片是同心雁S-ERP的操作界面截图,点击右侧“在线咨询”或者“立即试用”按钮,获软件系统演示方案~